Product introduction
The vacuum homogenization emulsifying unit consists of an emulsifying pot (with a lifting lid and a flipping pot body), a water phase pot, an oil phase pot, a vacuum device, a heating and temperature control system, a cooling system, an electrical control system, etc. The material passes through the polytetrafluoroethylene scraper on the mixing frame of the emulsifier in the homogenization pot, constantly creating new interfaces. Then, it is cut, compressed, and folded by the frame stirrer and the opposite stirring blades, and mixed to flow downwards to the homogenizer below the pot. Through the cutting, impact, turbulence, and other processes generated between the high-speed rotating rotor and stator, the material is cut in the shear joint and quickly crushed into particles of 200nm to 2 μ m. Material granulation, emulsification, mixing, blending, and dispersion can be completed in a short period of time. Due to the vacuum state inside the homogenization pot, the bubbles generated during the mixing process of the material are promptly removed. After the homogenization of the laboratory emulsifier is completed, raise the pot lid and press the pouring button switch to discharge the material inside the pot into the outer container (or open the pot bottom valve and pressure valve to discharge directly).
It mainly refers to the rapid and uniform distribution of one or more phases into at least one continuous phase using a high shear emulsifier in a vacuum state, which utilizes the strong kinetic energy brought by machinery to enable the material to withstand hundreds of thousands of liquid shear forces per minute in narrow gaps between the stator and rotor. Through the combined effects of centrifugal extrusion, impact, tearing, and other processes, the emulsion is instantly and uniformly dispersed. Through high-frequency cycles, high-quality products with no bubbles, fine texture, and stability are obtained.
The vacuum homogenizer emulsifier equipment is a non-standard customized equipment, which is reasonably configured according to the customer's process and suitable for products that require emulsification and stirring in a vacuum state. Can be equipped with low-speed scraping and stirring, used for emulsifying and stirring high viscosity products. Can be configured with a high shear emulsifier, suitable for processes such as dispersion, emulsification, homogenization, and mixing. The vacuum emulsifier is mainly composed of a water phase pot, an oil phase pot, an emulsion mixing main pot, a vacuum system, an optional lifting system, an electrical control system (PLC can be selected), an operating platform, etc.
The lid of the pot can be raised and lowered, and the material can be poured out. It can also be placed at the bottom of the pot for easy cleaning. Heating of materials is achieved by heating the conductive medium in the interlayer of the pot through an electric heating tube. The heating temperature can be set arbitrarily, and it is automatically controlled. Homogenization and stirring have time setting functions for easy operation. By inserting coolant into the interlayer, the material can be cooled, which is simple and convenient to operate. There is also an insulation layer outside the interlayer. Homogenization system and stirring system can be used separately or simultaneously. The part in contact with the material is made of medical grade 316L or 304 stainless steel, with a mirror polished inner surface and a hygienic vacuum stirring device.
Product features
The vacuum homogenizer emulsifier is a device that integrates functions such as vacuum defoaming, scraping and stirring, high shear homogenization and emulsification, heating, cooling, and electrical control. It is used for the production of medium and high-end pastes and high-density products.
Working principle
After the materials are mixed and reacted in the water and oil pots through heating and stirring, they are sucked into the emulsification pot by a vacuum pump. The center stirring and polytetrafluoroethylene scraper in the upper part of the emulsification pot always conform to the shape of the mixing pot, sweeping away the wall sticking materials, so that the scraped materials continuously produce a new surface. Then, through the cutting, compression, and folding of the blades, they are stirred and mixed and flow downwards to the homogenizer below the pot. The materials are then cut in the shear joint by the strong cutting, impact, turbulence and other processes generated between the high-speed rotating cutting wheel and the fixed cutting sleeve. The materials are quickly crushed into particles of 200um-0.2um. Due to the vacuum state inside the emulsification pot, the materials are generated during the mixing process. The bubbles were promptly removed. By using vacuum pumping, the produced products are no longer mixed with bubbles during the mixing process, thereby ensuring the production of products that are glossy, delicate, and have good ductility.
Performance characteristics
1. The emulsifying pot is an automatic lifting type, and the materials in the water and oil pots can be directly sucked into the emulsifying pot under vacuum through the conveying pipeline.
2. The discharge method is to heat the conductive medium inside the emulsifying pot to achieve heating of the material. The heating temperature can be set arbitrarily and automatically controlled.
3. Cold water can be introduced into the interlayer to cool the material, which is simple and convenient to operate. There is an insulation layer outside the interlayer. Homogeneous mixing and blade mixing can be used separately or simultaneously.
4. Material granulation, emulsification, mixing, blending, and dispersion can be completed in a short period of time.
5. The contact area with the material is made of stainless steel (made of 316L material for medical use) with a mirror polished inner surface. The vacuum stirring device is hygienic and clean, and the laboratory emulsifier is manufactured according to hygiene standards that comply with GMP regulations. It is suitable equipment for cream and cream production.
Application industry
1. Daily chemical and cosmetics industry: skincare cream, shaving cream, shampoo, toothpaste, cold cream, sunscreen, facial cleanser, nutritional honey, detergent, shampoo, etc.
2. Pharmaceutical industry: latex, emulsion, ointment (ointment), oral syrup, etc.
3. Food industry: thick sauces, cheese, oral liquids, baby food, chocolate, boiled sugar, etc.
4. Chemical industry: latex, sauce, saponification products, paint, resin, adhesive, detergent, etc.
Main components of the system
The vacuum emulsifier is mainly composed of a water phase pot, an oil phase pot, an emulsion mixing main pot, a vacuum system, an optional lifting system, an electrical control system (PLC can be selected), an operating platform, etc.
Performance and characteristics
♦ Our company produces a variety of vacuum emulsifiers, including homogenization systems with upper and lower homogenization, internal and external circulation homogenization, and stirring systems with unidirectional stirring, bidirectional stirring, and screw belt stirring; The lifting system is divided into single cylinder and double cylinder lifting, and various high-quality products that meet customer requirements can be customized;
♦ Triple mixing adopts frequency converter speed regulation, which can meet the production needs of different processes;
♦ Homogeneous structure, using double end mechanical sealing effect, high emulsification speed up to 4200 revolutions per minute, high shear fineness up to 0.2-5um;
♦ Vacuum defoaming is used to achieve aseptic requirements, and vacuum suction is employed, especially for powder materials, to avoid dust flying;
♦ The main pot lid can be equipped with a lifting device, which is easy to clean and has a good cleaning effect. The pot body can be used for pouring and discharging;
♦ The pot body is composed of three layers of stainless steel plates welded together, and the tank body and pipes are mirror polished, meeting GMP requirements;
♦ According to the process requirements, the tank can heat and cool materials, and the heating methods mainly include steam and electric heating;
Performance and configuration
1. The mixing adopts variable frequency speed regulation, allowing the mixing speed to be adjusted freely within 0-60 revolutions per minute to meet different process requirements.
2. Professional homogenizer with unique structure and high efficiency.
3. Easy to operate and use, with good emulsification and homogenization effect.
4. The German Fluke water circulation homogeneous sealing structure overcomes the problem of material leakage in ordinary seals; The sealing ring will not burn out in a high viscosity or material free state.
5. All parts that come into contact with the material are made of stainless steel, and the inner surface of the container is polished with a mirror of 300EMSH (sanitary grade), which meets the hygiene requirements.
6. Vacuum suction, vacuum defoaming, the entire process is completed in a vacuum state, without cell infection, extending the shelf life of the product.
Vacuum homogenizer emulsifier optional
There are two types of vacuum homogenizer emulsifier combination models to choose from, single emulsifying tank and emulsifying unit with oil-water pot, both of which can choose different power and stirring forms to achieve the desired performance.
Mixing form - The main pot is a frame type mixing and homogenization head, while the oil-water pot has anchor type mixing, dispersing disc, and blade type mixing.
PLC system - The PLC control system can not only control the equipment, but also connect with remote PC computers installed with automatic processing programs to optimize production time and save power.
Temperature measurement - temperature can be measured from the container wall, or the temperature measurement point can be located in the material in the mixing tank, moving with the revolution, with a temperature difference accuracy of ± 1 ℃.
Lifting methods - double column hydraulic lifting, single column hydraulic lifting, electric screw lifting.
Equipment form - experimental emulsifier, production emulsifier, etc.
Application area
Biopharmaceuticals; Food industry; Daily care products; Paint and ink; nanometer material; Petrochemical industry; Printing and dyeing auxiliaries; Paper industry; Pesticides and fertilizers; Plastic rubber; Power electronics; Other fine chemicals, etc.
Scope of application
Food: artificial butter, jam, mayonnaise;
Cosmetics: face cream, cream, lotion, toothpaste, dye paste, ionic perm, dioxygenated milk, etc;
Medicine: various ointments (dermatitis tablets), antibiotics, injections;
Comprehensive: resin coatings, paints, shoe polish, chemical fibers, etc;
Pharmaceutical industry: latex, emulsion, ointment (ointment), suppository, oral syrup, etc;
Chemical industry: latex, sauce, saponification products, paints, coatings, resins, adhesives, etc;
Food industry: sauces, cheese, oral liquids, baby food, chocolate, carbohydrates, etc;
Daily chemical industry: shampoo, shower gel, shampoo, laundry detergent, hand sanitizer, etc.
Product details
|
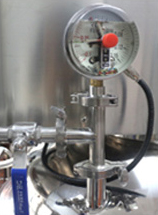
Vacuum meter |
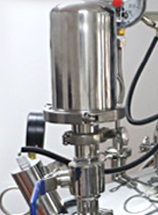
Air filter |
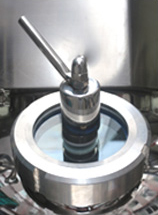
Wall scraping mirror |
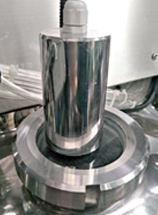
Lighting mirror |
|
|
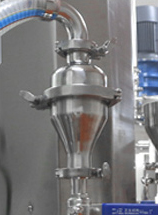
Materials Entrance |
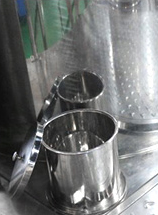
Spice entrance |
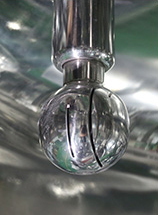
Spray ball |
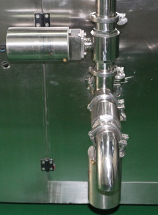
Outlet |
|
Product parameters
Emulsifying pot |
Model |
HRRHZ-250 |
HRRHZ-350 |
Design volume L |
250 |
350 |
Working volume L |
200 |
280 |
Mixing speed RPM |
0-65 |
0-65 |
Homogenizer speed RPM |
0-2800 |
0-2800 |
Lifting method |
hydraulic pressure |
hydraulic pressure |
Water phase pot |
Working volume L |
128 |
200 |
Mixing speed RPM |
1400 |
1400 |
Oil phase pot |
Working volume L |
105 |
150 |
Mixing speed RPM |
1400 |
1400 |
Total power |
Electrical heating |
42Kw |
48Kw |
Steam heating |
12Kw |
12Kw |