Product detail diagram
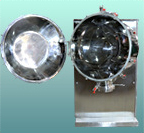
On the side of the equipment,
open the silo door |
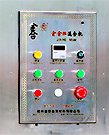
Control panel
|
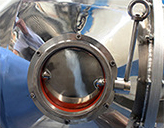
Quick installation butterfly
valve discharge port |
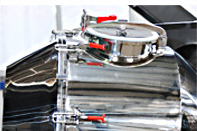
Quick opening feeding port
and silo opening |
The pharmaceutical and food type dual motion mixer is used in industries such as food, medicine, and additives. Compared with existing mixers on the market, this model has advantages in achieving a high degree of mixing effect on powders. It not only achieves macroscopic uniformity of powders (uniform sampling of powders in the upper, lower, left, and right directions inside the barrel), but also microscopic uniformity of powders (uniform dispersion between particles at the microscopic level).
Structural diagram of large dual motion mixer
Schematic diagram of powder flow in dual motion mixer
Given this structure, it is possible to achieve macroscopic uniformity, which means mixing uniformly in large areas, and microscopic uniformity, which means particles in small areas are directly and uniformly distributed. Macroscopic uniformity refers to the absence of blind spots in the mixing drum at the macro level. Some traditional mixer drums are fixed and only stirred by the blades, resulting in blind spots at the bottom of the drum; Macroscopic uniformity is also reflected in the sufficient uniformity of light and heavy powders, and light powders cannot be suspended without entering the main powder. Microscopic sufficiency refers to the requirement that the powder should be fully uniform within the particles of the powder within the microscopic range. If our raw powder is at or near the nanometer level, this requirement is higher, and ordinary mixers cannot meet this requirement, even if the mixing time is extended.
Structure diagram of dual motion mixer for medicine and food
Equipment specifications and dimensions
Model |
Material cylinder capacity
(L) |
Large loading capacity
(L) |
Drum speed
(r/min) |
Blade speed
(r/min) |
Motor Power
(kw) |
External dimensions
Length * Width * Height (mm) |
Whole machine weight
(kg) |
50 |
50 |
37.5 |
25 |
50 |
1.1 |
1400*620*1000 |
430 |
100 |
100 |
75 |
23 |
46 |
1.1 |
1450*720*1200 |
500 |
200 |
200 |
150 |
21 |
42 |
2.2 |
1550*860*1580 |
500 |
400 |
400 |
300 |
21 |
42 |
3.0 |
1800*1010*1600 |
910 |
600 |
600 |
450 |
17/14 |
34/28 |
3/5.5 |
2300*1120*1750 |
1200 |
800 |
800 |
600 |
14 |
28 |
5.5 |
2500*1200*1850 |
2000 |
1000 |
1000 |
800 |
11 |
22 |
7.5 |
2880*1350*1900 |
2300 |
1500 |
1500 |
1200 |
8 |
16 |
15 |
2890*1870*2240 |
2600 |
Specifications above 1500 can be customized according to specific customer needs
Advantage
The practical advantage is that it is easy to clean
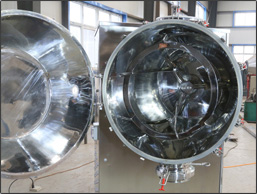
The silo has a full-size large door for easy cleaning and
prevents cross infection of powders |
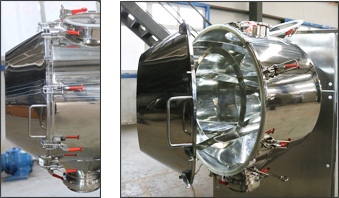
The large door of the silo is fastened with a buckle,
making it easy to open and close, and can be operated in 1 minute |
Eight advantages of dual motion mixer
1. The mixing uniformity is particularly high
Due to the use of dual motion superposition mixing technology, it is possible to achieve macroscopic uniformity - that is, to allow the powder to roll up and down, and to diffuse and mix evenly through left and right convection; It can also repeatedly interweave and shear particles in multiple layers and directions at the microscopic level of the powder, achieving precise and forced mixing. So the mixing uniformity can reach the realm of macroscopic uniformity and microscopic ultra-fine uniformity.
2. The mixing efficiency is particularly high
This is also because of the principle of superposition and mixing of two movements. When two movements are carried out simultaneously per unit time, not only does it double the mixing efficiency, but it also promotes the mixing effect perfectly and effectively promotes the mixing work. Therefore, the dual motion mixer saves 60% of time compared to traditional mixers.
3. Meet the requirements for fine mixing of ultrafine powder
The above picture shows the floating phenomenon of 3000 mesh coating powder when it falls freely
An important characteristic of high-tech materials and ultrafine materials is their small size, sometimes even down to the nanometer level, so that gravity almost loses its restraining force on them, and they can float when obtaining a small amount of kinetic energy, making mixing work difficult. In traditional mixers, intense mechanical kinetic energy can transfer energy to the powder, causing various activities in the powder, overcoming gravity to produce phenomena such as floating, adsorption, and repulsion, resulting in mixing difficulties.
The core principle of the dual motion mixer is to perform medium low speed, multi-layer shear mixing in low-speed flowing powder. The mechanical impact, friction, and kinetic energy generated by it are very small, which suppresses the floating, adsorption, repulsion, and other activities of the ultrafine powder, allowing the mixing work to proceed smoothly.
4. Effectively solve the problem of difficult mixing of light and heavy powders
The difficulty in mixing light and heavy powders evenly in traditional mixers is a typical mixing process challenge. This is because in the gravity diffusion mixing of powders, due to the significant difference in weight, light powders are often suspended above the main powder, making it difficult to mix into the main powder. Even if the mixing time is extended, it is difficult to solve the problem.
The use of a dual motion mixer can effectively solve such problems, as shown in the left figure. Due to the fact that the dual motion mixer stacks rotating internal blades inside a rotating container, with the same direction and faster speed. In this way, the container and blades will carry the floating light powder into the main heavy powder, allowing the light and heavy powders to be evenly mixed.
5. Less damage to the original appearance of the powder after uniform mixing
Many industries require that the shape and size of the powder remain unchanged or minimally changed after mixing, in order to achieve precise control over the overall process. Dual motion mixers can do a good job in this regard.
This is because the core principle of the dual motion mixer is to perform multi-layer, multi-directional, and low-speed shear mixing in the low-speed flowing powder. The mixing motion is smooth and orderly, without powder impact or high-speed impact. In addition, the mixing time is greatly shortened, which can protect the powder shape from being basically unchanged.
The figure on the right shows the changes in the appearance and shape of the powder after mixing by measuring the specific gravity and average particle size of the material.
6. Equipment loading rate up to 80%
The main mixing work in the dual motion mixer is completed by the internally moving spiral blades, so the remaining space in the material bucket can be very small. Therefore, even with a high loading rate, the equipment can still perform the mixing task well.
Therefore, the loading capacity of the dual motion mixer is increased by more than 50% compared to traditional mixers.
7. To save money
Due to the use of professional technology, the movement of the material barrel and the movement of the blades superimpose and mix the materials, resulting in significant economic benefits for the dual motion mixer while improving the mixing quality.
1) Reduce mixing time by 50%;
2) Reduce motor configuration by about 30%;
3) Due to high loading rate, the equipment has a small size and saves space.
8. Exemption from the equal incremental mixing method of trace elements
The traditional mixer has poor mixing ability, which restricts the uniform mixing of trace elements. Therefore, a complex mixing method of manually feeding equal amounts in batches and steps is often used to overcome equipment defects and achieve uniform mixing of trace elements. The mixing ability of dual motion superposition mixing can completely mix trace elements in one go. Time saving, labor-saving, uniform and reliable, and not prone to errors.
In the food, additive, and pharmaceutical industries, due to the generally poor flowability of powders, almost half of the powder mixing uses the trace element equal increment method, which is a huge burden for enterprises. The use of dual motion mixing can save enterprises a lot of manpower, material resources, and valuable time.
Compared to traditional mixers
Dual motion mixer
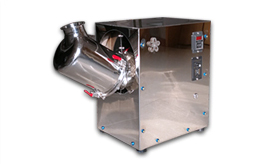
Comparative advantages:
1. Fine mixing to achieve microscopic uniformity
2. Ultra light powder and ultrafine powder can also be mixed evenly
3. Save time, energy, and install more
4. Stable and safe operation at a constant speed
5. Large scale machines capable of producing 5000 liters or more
6. The material bucket can be easily opened at large diameters
Thoroughly clean the residue inside the material bucket without any dead corners
3D mixer
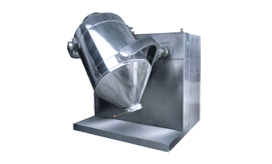
Shortcomings in comparison:
1. Difficult to achieve precise mixing
2. Ultra fine powder and ultra light powder are not easily mixed into the main powder
3. Long mixing time, high power consumption, and low loading rate
4. High acceleration during operation, with unsafe records of broken shafts
5. Due to safety concerns, we are unable to produce large-scale and heavy tonnage models
Dual motion mixer
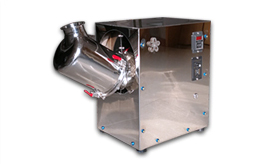
Comparative advantages:
1. Ultra fine mixing achieves uniformity between particles
2. Can solve the mixing problem of ultra light powder and ultrafine powder
3. Constant speed operation saves time, energy, and requires more installation
4. The material bucket can be easily opened at large diameters,
Thoroughly clean the residue inside the material bucket without any dead corners
V-mixer
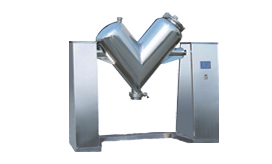
Shortcomings in comparison:
1. The powder at the microscopic level is not easily uniformly distributed
2. Ultra fine powder and ultra light powder are not easily mixed into the main powder
3. There is gravity lifting motion, so the power consumption is high
4. There is throwing and smashing motion that can damage the shape of the powder
Dual motion mixer
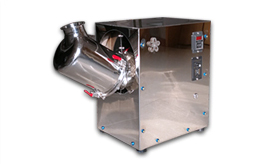
Comparative advantages:
1. Sports material bucket has no dead corners for materials
2. Low equipment load during mixed operation, saving time and electricity
3. The material bucket can be easily opened at large diameters,
Thoroughly clean the residue inside the material bucket without any dead corners
Ribbon mixer
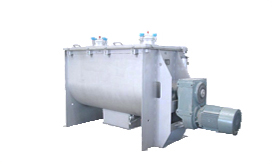
Shortcomings in comparison:
1. If the material bucket is fixed, there may be blind spots for materials
2. The startup load of the equipment is particularly large,
Difficulty starting at full load, time-consuming and electricity consuming
3. There are residues in the discharged material